Author: admin
Lots of glassing on the interior
Finishing up the cabin roof
A major milestone: putting on the cabin roof
This went basically according to plan: I put 3 coats of epoxy on the underside of the two pieces, glued them together, and carefully checked its fit on the hull. I used lots of glue and temporary screws, working quickly to get it all done before the epoxy started setting up. Afterwards I used a router and a plane to trim off the excess.
This was the last major component to be added to the hull. The next steps are a lot of filleting on the cockpit, lots of sanding all over the upper hull, and glassing the entire cockpit and cabin roof.
A brief diversion: cutting the bowsprit
I cut it with a bandsaw (which made a rather wavy cut), and got it flat with a plane.
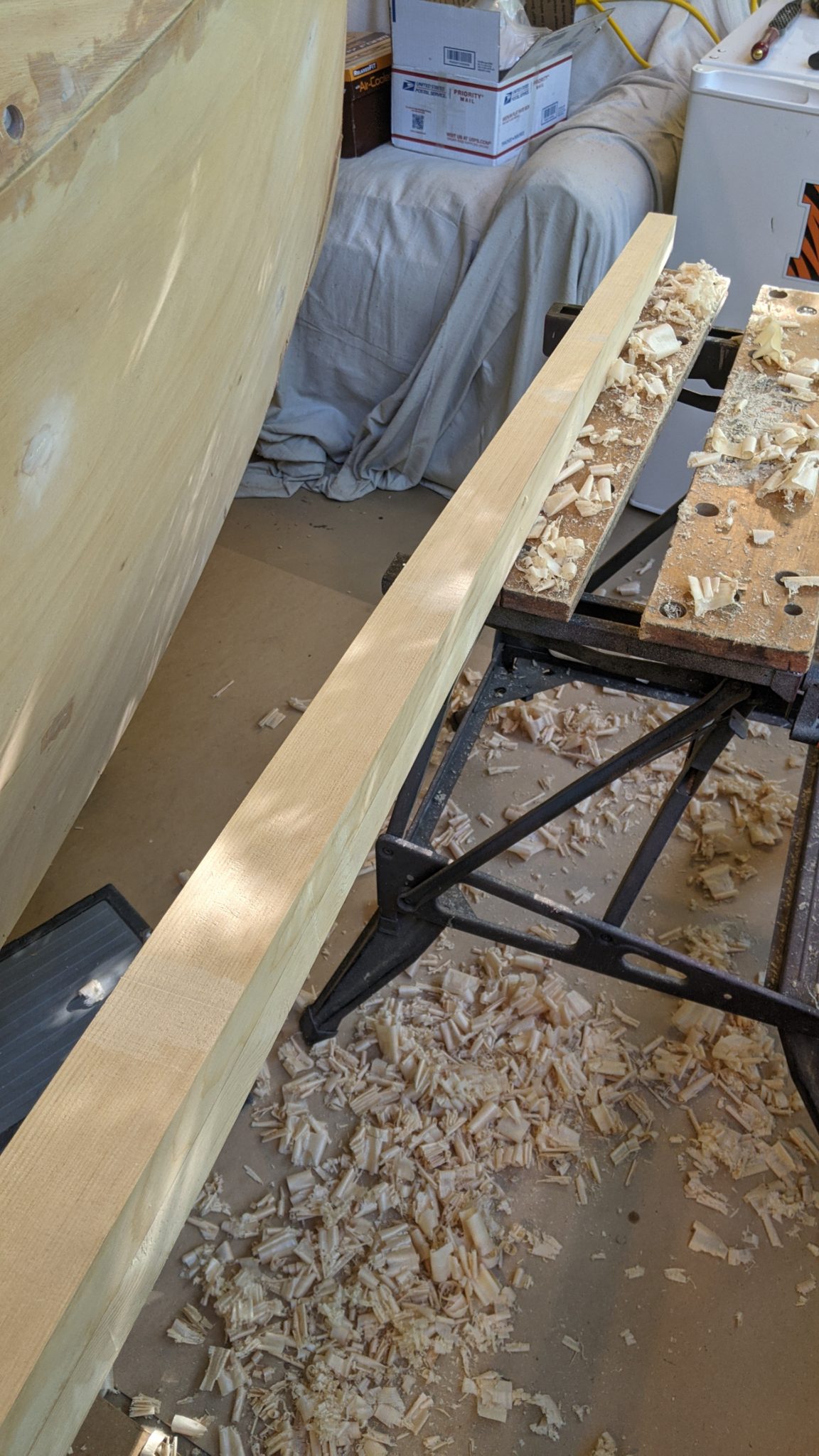
Attaching a lot of stuff to the front of the boat
Bending and clamping strips of wood
Finishing the seatbacks
I cut lots of pieces of styrofoam insulation and put them in the buoyancy chambers. I also primed and painted the storage compartments at the rear. Next I glued the seatback panels into place. They are held in place with clamps, stainless-steel pneumatic brads, and a couple of weights. The last step was to glue down the top pieces.
The current state of things
The transom skirt, and steam-bending
I installed the transom skirt:
I decided that the forward sheerclamps were too stiff to successfully bend into place, so I decided to steam them first. I made a minimalist steam box from an empty paint can and seven feet of “spa vacuum hose” from Lowe’s. For a heat source, I naturally used the same LP gas burner I got for the lead-melting. After an hour of steaming, each sheerclamp bent easily, and I clamped them to the outside of the hull to dry out for a few days.
Zipping right along on the upper hull!
Installing the upper hull pieces
Installing the footwell and main deck
Below is a shot of the centerboard pendant sheave, safely tucked away in the trunk. I 3D-printed the spacers on either side of the sheave.
Floorboards all done!
Finishing and installing the floorboards
I have been finishing the floorboards with Danish Oil. It is slow work. Because the stuff is stinky I have to work in the cold garage, so the Oil needs a long time to dry. So far about half of the floorboards are installed, and the rest need one more coat of Danish Oil.
I also finished the centerboard trunk with several coats of clear water-based polyurethane. People will be able to look at it and know for sure that this is a wooden boat!
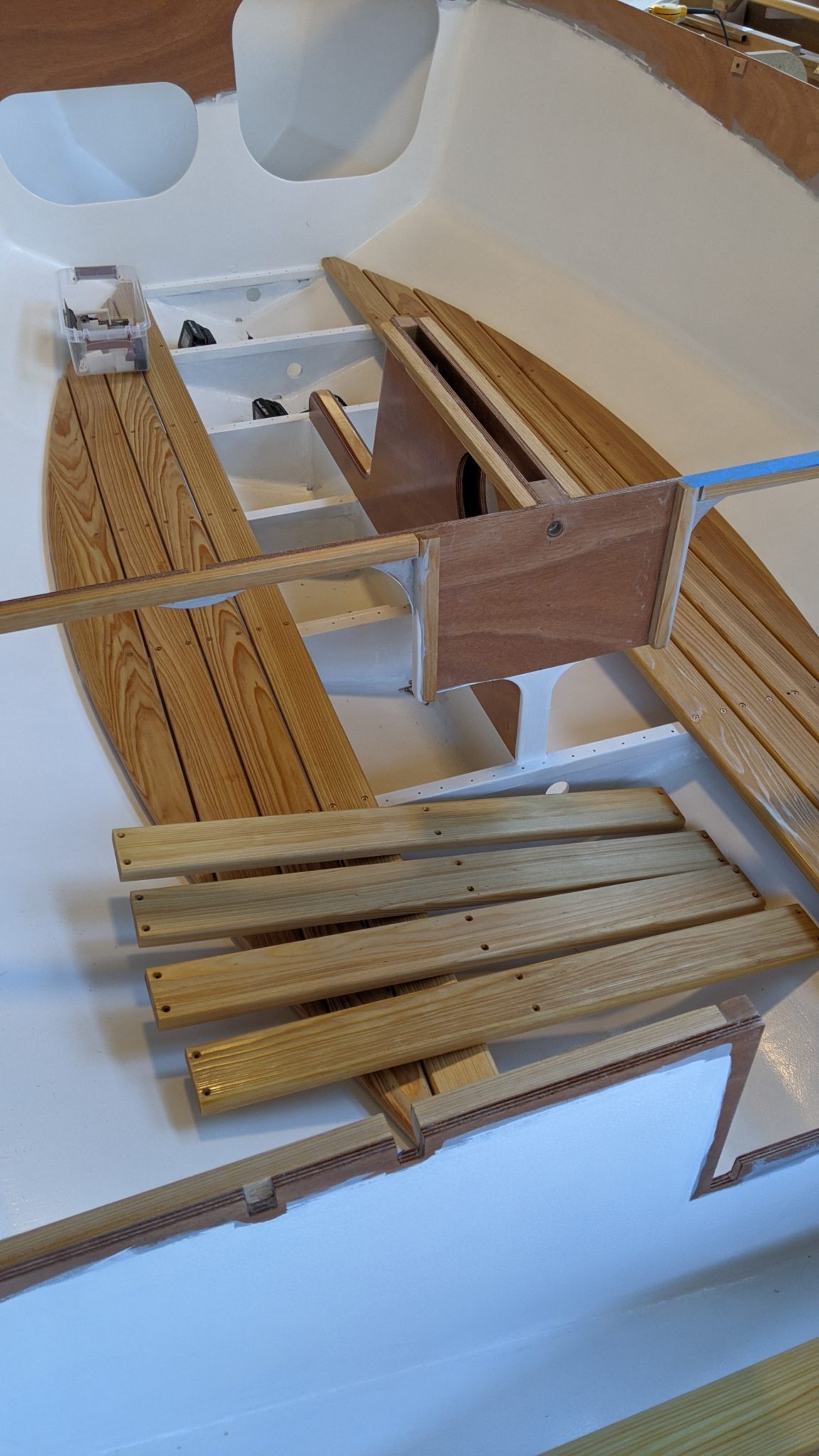